Retrofit Underfloor Heating
With adaptable solutions for all kinds of renovation projects, underfloor heating is a great way to enhance the efficiency and comfort of your project.
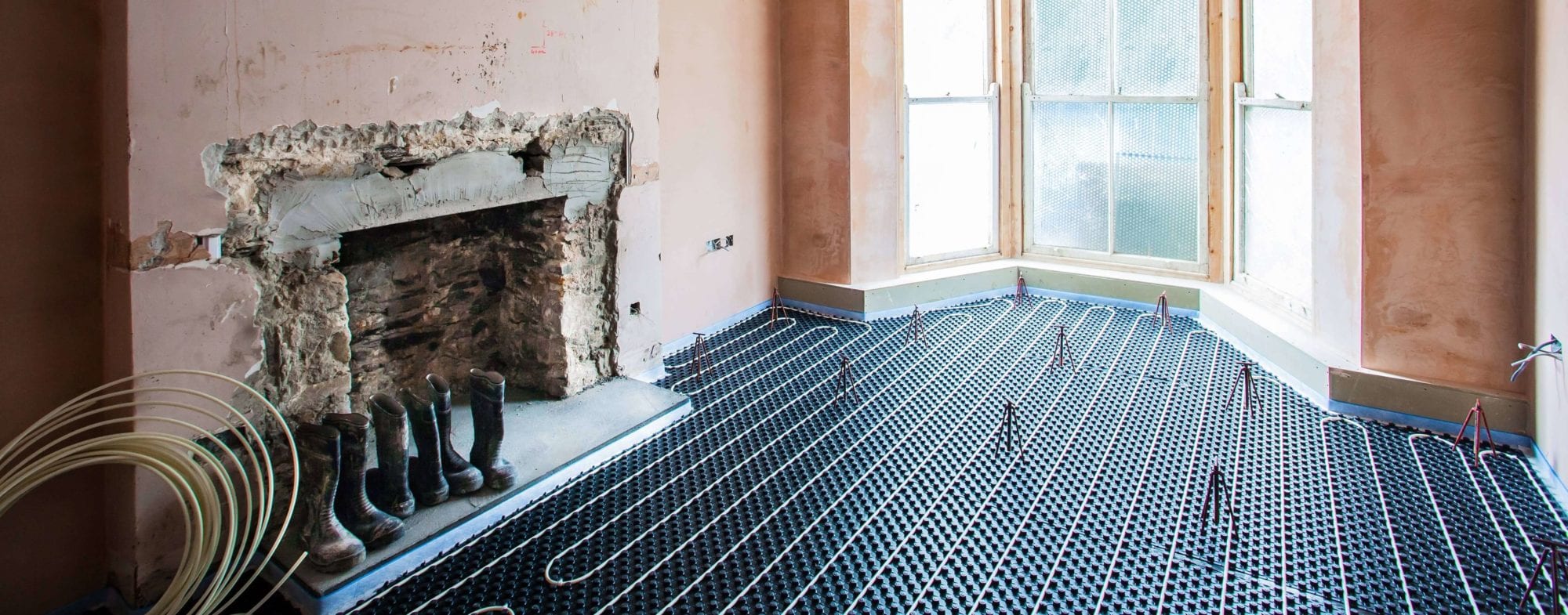
Considerations for a successful retrofit underfloor heating installation
To maximise the benefits of underfloor heating in a renovation project, it’s important to take a tailored approach. Unlike new builds, older properties often present unique challenges due to varying insulation levels and floor constructions.
Consulting with an expert will help combat these challenges and simplify the decision-making process. They will advise on key factors including system options, design, and steps you can take before installation to optimise the performance of an underfloor heating system.
Minor Cosmetic Work
For renovations focused on cosmetic improvements like painting and decorating, there is generally less disruption involved. Systems that are installed over the existing floor, like those from our LoPro® range, can keep this level of disruption to a minimum.
When selecting the right overlay system, consider how much floor height build-up is available and existing insulation levels. These elements can significantly influence the suitability of systems.
Extensive renovation
In a large-scale renovation, involving significant structural changes, such as removing walls or adding extensions, major works may already be part of the plan, reducing the number of additional considerations. The project is also likely already compliant with current building regulations, meaning existing insulation levels are usually suitable for a wider range of underfloor heating options.
Structural or screed systems can be excellent choices for major renovations, depending on the specific scope of work. To explore these options further and find the best fit for your project, use our UFH Selector Tool.
Keeping the existing floor structure
If the renovation project doesn’t involve replacing the existing floor, overlay systems provide a great solution for installing underfloor heating.
However, you may want to consider additional factors such as insulation levels and the amount of floor height build-up available here, as this can have a big impact on which system is most suitable and whether further alterations are needed prior to UFH installation.
Changing the floor
If the floor structure is going to be changed, it could be worth considering an integrated system, for minimal or zero height build-up. To see which of these systems might be best suited to your project, try using our UFH selector tool to find the right system.
Where possible, it’s also worth using this opportunity to add insulation beneath the floor, to improve the comfort and efficiency of the home.
Solid Floors
For solid concrete floors, overlay systems are often the most effective solution. As solid concrete minimises downward heat loss, additional insulation is not typically necessary. This approach eliminates the need for disruptive and costly floor excavation.
With many different overlay systems available, it’s important to consider which might be best suited to your project. You can use our UFH selector tool to decide.
Joisted Floors
A range of options are available for retrofitting underfloor heating on joisted floors. With some that can even be installed between joists, ensuring minimal disruption and height build-up.
When considering underfloor heating for joisted floors, it’s important to assess and, where necessary, improve, the existing insulation levels to prevent heat loss. Along with a bespoke design, optimal insulation will ensure an underfloor heating system performs as expected.
Find the right UFH system for your project
Use the Underfloor Heating Selector Tool to find the right system for your project.
Other considerations for retrofitting UFH
For more considerations that will help you successfully retrofit underfloor heating, read on.
Is the heat source being changed?
Different heat sources can interact with underfloor heating differently, whilst renewable solutions such as heat pumps produce the low flow temperatures most compatible with underfloor heating, a good system design can ensure underfloor heating works with almost any heat source.
If you are considering whether a heat pump would be the right heat source for your project, take a look at our HP qualifier tool to find out in seconds if a heat pump could work for you.
Which underfloor heating system is best suited your project?
Which underfloor heating system would be best suited to your renovation can vary based on the specifics of your project. While there are a wide variety of systems available, to find out which one could be right for your project use our underfloor selector tool, or call us to speak to one of our experts today.
Budgeting for a retrofit underfloor heating renovation
The cost of a retrofit underfloor heating system can vary depending on the system used and size of the project. The best way to get an accurate idea of the cost involved, is to get a free, no obligation quote from a supplier.
How to install UFH in a retrofit project
With the right support and a thorough design, retrofitting underfloor heating is easier than you might think.
Nu-Heat helps keep the process simple by connecting homeowners with qualified local installers and providing industry-leading installation manuals and expert technical support for both installers and self-builders.
The importance of UFH design
A well-designed underfloor heating system is crucial for any project, but is especially important in renovation scenarios, where existing insulation and glazing must be considered to ensure the system performs as expected.
To be sure that the design you’ve received will aid the performance of the system, check that your supplier has included bespoke calculations such as room-by-room heat losses to tailor the design to the needs of your renovation.
Choosing the right underfloor heating supplier
Selecting the right underfloor heating supplier is crucial.
A good supplier will guide you through the specification process, ensuring you choose the right system for your project. They will also create a bespoke design, factoring in room-by-room heat losses, glazing, and insulation levels, to design a system that meets your project’s specific needs. Then, once the system is installed, they should provide ongoing technical support, to ensure the system continues to performs throughout its lifetime.
To ensure you choose the right supplier, enquire about their approach to system design and the level of support they provide as standard once installation is complete.
Want help finding the right underfloor heating solution?
We would love to speak with you to discuss your project. If you have a question about your existing Nu-Heat system, our technical support team are at hand.
Retrofitting underfloor heating FAQs
Can you install underfloor heating on top of tiles?
Yes, if the tiles are structurally sound, an overlay system can usually be laid on top of them. However, you should always check this with a qualified person on site as this can vary on a case-by-case basis.
Can you install underfloor heating in an existing house?
Yes, Nu-Heat have an extensive range of retrofit underfloor heating options designed specifically for renovation projects.
Can you install underfloor heating on a concrete floor?
Yes, Nu-Heat’s overlay systems are designed to be installed directly over various kinds of existing floors, including concrete.
Can you install underfloor heating on wooden floorboards?
Yes, as long as they are structurally sound and level. We would always recommend that any suspended ground floors with an air void below should be insulated to reduce downward heat loss.
Does underfloor heating raise floor level?
Nu-Heat offer a range of products, such as our in-between joists and screed systems, which don’t add any height to the floor level. And if these products aren’t right for your project, we also have a variety of systems that offer minimal height build up on top of the floor, as low as 15mm.
Can underfloor heating be retrofitted?
Yes, Nu-Heat have a dedicated range of retrofit underfloor systems that are designed for renovation projects.