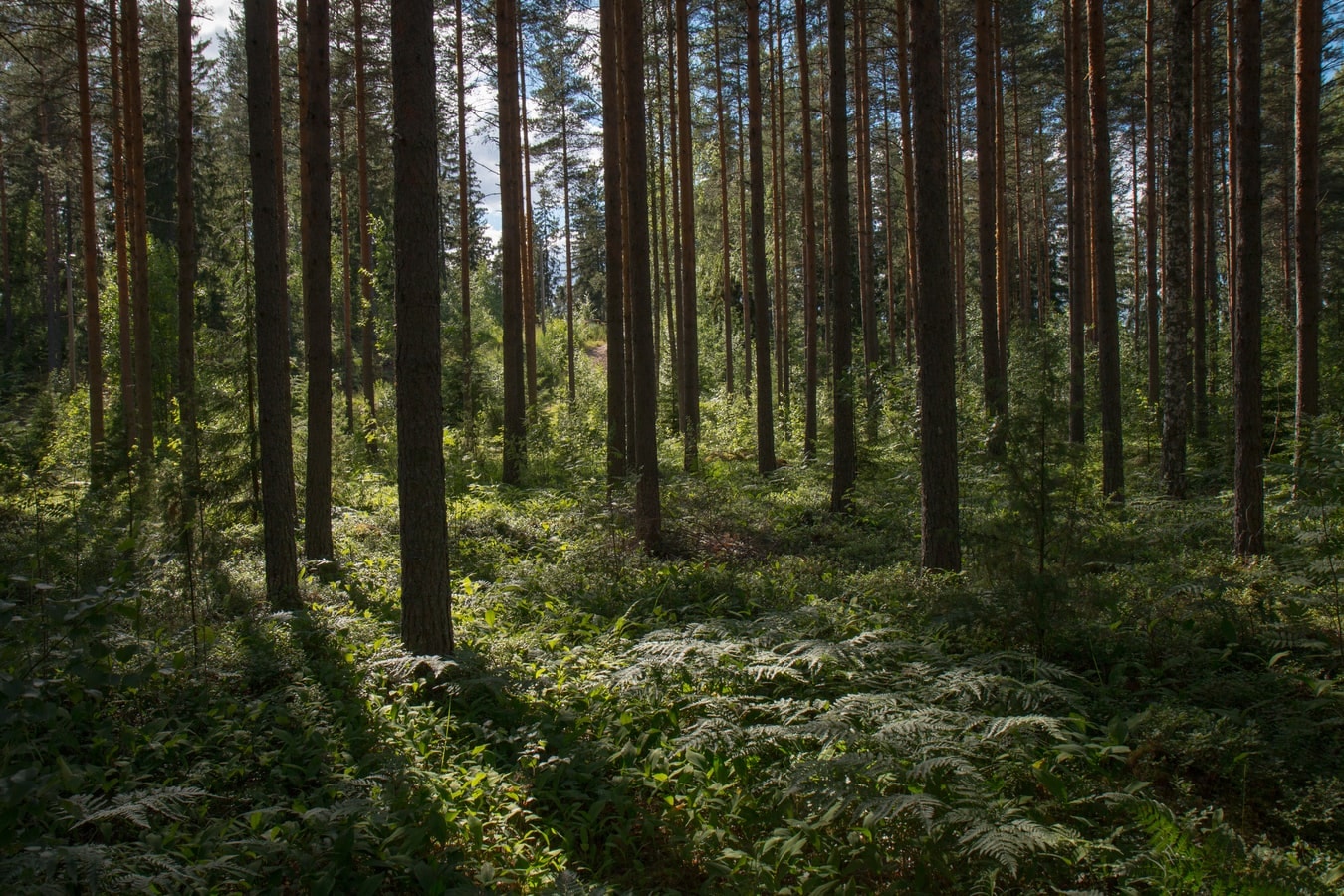
What is the Decarbonisation of Heat?
The decarbonisation of heat refers to reducing the amount of carbon produced by heating systems. This involves switching to low carbon heating systems in order to provide homes with ‘clean’ heat.
Why do we Need to Decarbonise Heat?
Heating is one of the biggest sources of carbon emissions in the UK, contributing to global warming. The decarbonisation of heat is a must in order to significantly reduce the UK’s carbon emissions in line with the goals set out by the Government to reach net-zero by 2050.
How to Decarbonise Heat
Decarbonising heat is not without its problems, however. It is going to be extremely difficult to do and will require reform on a large scale.
Earlier this year Nu-Heat commissioned a report on the challenges of decarbonising heat in the UK’s housing stock. It looks at the various challenges related to the decarbonisation of heat, the potential benefits of decarbonising heat and suggests policy changes to support the move to low-carbon heating alternatives.
REPORT: Decarbonising heat – supporting the UK’s move to low-temperature heating
DOWNLOAD REPORT HERE | VIEW INFOGRAPHIC
Executive summary
The UK has set the ambitious target of reaching net zero emissions by 2050. To reach this, heat from buildings will need to be decarbonised in a short timeframe.
The UK Government should support the installation of more efficient, low temperature heating systems. This is a no-regrets option. Underfloor heating (UFH) systems are the most efficient emitters which can be used with electric heat pumps and other renewable heating units. UFH systems have efficiency, space saving, comfort, air quality and health and safety benefits when compared to radiators.
Underfloor Heating is low temperature heating by design.
To support UFH deployment in the UK, the Government should:
1. Develop the revisions to Part L and Future Homes Standard based on 45°C flow temperature wet central heating systems rather than 55°C.
2. Maintain standards (e.g. MCS) to ensure that consumers have the confidence to invest in heat pumps and UFH systems. These need to be properly designed, specified and installed. Installer training is therefore also key, and should be supported by Government.
3. Amend SAP to better reflect the additional benefits of UFH over traditional radiators. Reflect the move to low temperature and more consistent heating patterns in SAP
1. Context – the move to low temperature heating
The UK must decarbonise buildings if it is to reach its 2050 net zero target. Residential buildings account for 15% of the UK’s greenhouse gas emissions, and whilst much progress has been made in decarbonising energy supply (see comparative trends in figure 1 below), progress in reducing emissions from homes has floundered.
Figure 1 – comparison of the change in UK sectoral emissions 2013-2018 (source: BEIS)1
Emissions from buildings can be reduced in two ways, by reducing the amount of energy needed, and by decarbonising the supply of energy into the home. Given the scale of the challenge, the UK will need to simultaneously improve the energy efficiency of buildings and green the energy supplied to homes and businesses. A ‘wrap then heat’ process to tackling energy demand and supply.
On the supply-side, the shift to green electric heating offers an opportunity to reduce emissions from buildings. The UK has made fantastic progress in reducing emissions from the production of electricity, with the establishment of solar and an internationally renowned offshore wind industry. This progress will continue over the coming years, with offshore wind projected to provide a third of the UK’s electricity needs by 2030.
On the demand-side, whilst there has been some progress on delivering energy efficiency measures, more can and should be done. Indeed, as illustrated in figure 2, over 7 million solid wall and 5 million cavity wall properties could be further insulated – many of them cost-effectively.
Figure 2 – current technical and cost-effective energy efficiency retrofit potential, as at 2015 (UKERC, 2017)2
Energy efficiency is a crucially important part of the heat decarbonisation challenge. Reducing the amount of energy needed to heat a home comfortably, makes sense on economic, environmental and social terms – and helps to address energy poverty and climate change simultaneously.
Ensuring that homes are energy efficient is also an important step in making the building stock ‘renewables-ready’. Electric heat pumps are a very efficient renewable heating technology that will play a crucial role in the decarbonisation of heat. Sweden has over 1.6 million heat pumps in operation and 91% market share against boilers (as a % of their combined sales), France (over 2 million), Denmark and other European countries have already successively supported mass-market uptake of heat pumps, which operate with very low emissions.
These technologies operate optimally when installed in energy efficient properties. Costs to consumers are reduced through lower energy bills and as a result of smaller heat pumps being specified. When installed in an efficient building which has been made renewables ready, the heating system can be operated at a lower flow temperature. This improves the performance of the heat pump, lowers emissions and saves consumers money.
To operate effectively at low flow temperatures, heat pumps need to be twinned with large heat emitters – such as large radiators, or more optimally underfloor heating (UFH). Such large heat emitters have the additional surface area to ensure that the same amount of required heat is delivered to rooms. Therefore, the room can be heated to the desired temperature using cooler water in a wet central heating system. This is ultimately more efficient and uses less energy.
2. Importance of new-build properties
At current rates, nearly 2 million homes will be built in the UK in the 2020s3, with the Conservative Party manifesto suggesting this number could be boosted closer to 2.5 million. These properties will still be standing in 2050, it is therefore crucial that they are built to a standard that is consistent with a pathway to zero-emissions. Where possible and cost-effective, renewable heating systems should be installed today. For those properties that install a non-renewable system, as a bare-minimum they need to be ‘renewables ready’ to allow for a seamless transition to low emission heating.
The decarbonisation of power production in the UK and efficiency of electric heat pumps make this technology well-placed to lower emissions when installed in new buildings. Getting supportive regulation for heat pumps in new-build properties right is important, as this is where the technology is immediately cheapest to install and typically most cost-effective. A thriving mass-market for heat pumps needs a healthy installer-base and supply chain to sell renewable heating technologies and install systems. The heat pump industry sees new-build properties as an important first step for wider adoption of the technology in the UK4.
Fortunately, UK policymakers are pushing new build regulations in the right direction. The proposed uplift to Part L (fuel and power) and Part F (ventilation) includes improved energy efficiency standards, steps taken to phase-out fossil fuels (removal of fuel factors), and changes which generally support renewable heating systems.
However, given the announcement of the UK’s net-zero target, it is clear that the Government needs to reduce emissions from buildings to close to zero by 2050. In the consultation, pushing the uplift of Part L further to the package of reforms that delivers a 31% reduction on CO2 emissions rather than only 20% is the way to go. For new buildings, it is important to ensure that each opportunity to cost-effectively tighten regulations and support renewable heating systems is taken.
3. A cost-effective move to low temperature heating
In this respect, the revision to Part L is in danger of not going far enough. The revision currently proposes that wet central heating systems should be designed to operate at 55°C flow temperature. This is not ambitious enough, and misses the opportunity to better support, low-cost, efficient heating through optimal heat pump performance.
Moving homes to low temperature heating is one of the true no-regrets actions that the UK Government can take to support the decarbonisation of the building stock. Whilst there are significant and challenging policy questions to consider relating to the technology pathways most suited to diverse building types and consumer preferences, the move to more efficient, lower temperature heating systems can provide energy and carbon savings across the board. As BEIS recognise5, hydrogen-heating, electric heat pumps and bioenergy boilers are likely to all play a role in the decarbonisation of heat. The move to low-temperature systems will improve the efficiency of all technology options and therefore the costs of the energy transition.
Electric heat pumps certainly operate best at low flow temperatures. Figure 3 considers the electricity required to power an ASHP over its lifetime in a typical new-build semi-detached property at two different flow temperatures. The proposed flow temperature of 55°C is compared to our suggested level of 45°C.
Figure 3 – impact of lower flow temperature on final energy demand of ASHP
In the 45°C scenario the electricity consumption of the ASHP is approximately 5 MWh lower over its lifetime. Figure 4 uses BEIS price electricity projections to translate this energy consumption decrease into an energy bill saving. Over the lifetime of the ASHP, the lower 45°C flow temperature specification saves the household over £900.
A move to lower flow temperature heating also ultimately saves carbon emissions. Taking account of the declining carbon intensity of electricity between 2020 – 2038, the targeting of a 45°C flow temperature saves just under 0.5 tonne CO2e per property. Aggregating this up over 250,000 new build homes (roughly equivalent to the new build target) and making a conservative assumption that 50% have wet central heating systems and ASHPs installed, those properties would save a total of 55,000 tonnes of CO2e over 18 years.
Monetising this using the Government’s cost of carbon and coupling with the fuel bill reductions over the period gives a saving to the UK
economy of over £118 million.
Figure 4 – impact of lower flow temperature on lifetime fuel bills of ASHP
Whilst the benefits of operating a heating system at a lower flow temperature are clear, the costs need to be considered. Figure 5 below takes the fuel bill savings achieved by operating an ASHP to 45°C flow temperature rather than 55°C and compares this with the additional cost of installing large heat emitters. Here, underfloor heating (UFH) has been installed at an incremental cost over typical, small radiators – see appendix for cost assumptions.
Lifetime fuel bill savings amount to £941, which more than cover the additional cost of UFH (£683) to give a net saving of £258. Note that – at an 18-year ASHP lifetime – this is a conservative estimate of benefits accrued over the total lifetime of the building but is more reflective of the benefits that can be enjoyed by a single occupier. In reality, the net savings over the lifetime of the building will be higher.
Figure 5 – incremental cost and fuel bill savings of UFH against small traditional radiators in a new build property
This analysis demonstrates that it is cost-effective to target lower flow temperature heating in forthcoming revisions of building regulations, and specifically 45°C should be targeted rather than 55°C.
Wet central heating systems are installed in the vast proportion of new build properties and should be favoured in many more under the proposed Part L revisions. Table 1 provides results of modelling which compares the cost-effectiveness of an ASHP which utilises a wet central heating system, with direct electric panel heaters which do not, at several energy efficiency specifications and building types.
What table 1 shows is that ASHPs should continue to play an important role in new build properties based on their cost of installation and operation (‘cost effectiveness’), and even in very energy efficient buildings.
It is therefore important that the UK Government ensures that the opportunity to cost-effectively lower flow temperatures to 45°C is taken in the forthcoming revisions of building regulations.
Table 1 – lowest cost: direct electric panel heater or ASHP?
Small flat (50m²) | Large flat (70m²) | Semi-detached (83m²) | Detached (117m²) | |
2013 Part L Notional (default) | ASHP | ASHP | ASHP | ASHP |
30kWh/m²/year space heating | Panels | ASHP | ASHP | ASHP |
25kWh/m²/year space heating | Panels | ASHP | ASHP | ASHP |
20kWh/m²/year space heating | Panels | Panels | Panels | ASHP |
15kWh/m²/year space heating | Panels | Panels | Panels | ASHP |
Policy ask #1
Electric heat pumps are the lowest-cost electric-heating solution for most new-build properties, supporting energy efficiency and very low emissions. It’s crucial that the UK Government takes each opportunity to support their deployment.
MHCLG should develop the revisions to Part L and Future Homes Standard based on 45°C flow temperature wet central heating systems rather than 55°C.
4. Underfloor heating as the optimal solution
It is crucial that building regulations are developed so that heating systems installed in new build properties operate efficiently at low temperatures. Large heat emitters are an important component of low temperature systems. These often take the form of large radiators or alternatively underfloor heating (UFH) systems.
Whilst any low temperature heating and heat emitter system is preferable to the high temperature systems currently installed, there are several reasons why policymakers should be supporting UFH as a superior solution over large radiators. These features become more important as the UK shifts to low temperature heating in response to its climate change objectives, and by its very
nature, underfloor heating is low temperature heating.
UFH operates beneath the floor and heats rooms using a greater proportion of radiant heat than typical radiators. Systems are typically powered by either electrical floor mats, or warm water – as with wet central heating systems. Electrical UFH, though at times used in small areas in homes for convenience, is comparatively expensive to run and typically at least 4 times more costly to use than a wet UFH system.
Wet UFH systems are therefore the most cost-effective, and well-placed to support the deployment of heat pumps in the UK, as they operate effectively at low flow temperatures and offer a large surface area for heat distribution – conditions which are well-suited to efficient operation of heat pumps.
One of the challenges with a mass-electric heat pump rollout is the consequences for the power grid, where supply and demand needs to be matched in real-time. UFH can also support with the type of dynamic operation of heat pumps that will lower the UK’s cost of decarbonisation6. UFH offers a type of thermal battery that allows a property to shift their load from peak times to less expensive hours of the day. This flexibility is a valuable asset that can be unlocked by installing UFH.
It’s important to emphasise that UFH systems are low temperature by design and can be utilised with a range of low carbon heat sources, including hydrogen and biomass boilers. Indeed, the move to underfloor low-temperature heating is a no regrets step which is aligned with several heat decarbonisation pathways. Whilst the benefits for electric heat pump operation are substantial and relevant to the Part L newbuild consultation, UFH installation would also support the efficient running of other hydrogen and bioenergy heating systems. As these energy sources are likely to be relatively scarce and costly, it’s important to use such resources efficiently to lower the cost of decarbonisation for the UK economy.
The benefits of UFH over larger radiators are explored below:
(a) Comfort and energy savings
In practice, it is common to see UFH delivering energy savings against the equivalent large radiator system. This is driven by two factors, firstly there are technical reasons why UFH delivers energy savings against radiators, and secondly there are behavioural responses to the improved comfort and feel.
Figure 6 below shows the results from a simulation of the energy consumption of a reference new-build property, heated using either UFH or radiators. This simulation was calibrated using actual field-trial evidence in a very efficient nZEB (near to zero energy building) test facility in Tallinn.
Here, the UFH system delivers the set point temperature in the new-build property at a lower energy demand than the radiator. In the study, this was found both amongst older, less efficient houses (where the savings were even more pronounced) and newer buildings. The study suggests that at a technical level, the UFH system can reach the desired set point temperature in the house more efficiently than a typical radiator setup.
Figure 6 – annual heating energy usage in a new building (Source: Vosa et al, 2019)
Secondly, occupants can feel the warmth radiating from the floor with UFH. There is undoubtably a psychological aspect of feeling the warmth emitted by UFH on the soles of your feet. One of the common challenges that consumers often have with low temperature heating and heat pumps is that they can’t feel the warmth in the radiators in the same way that they could with high temperature, gas boiler-driven systems. The radiant heat produced by UFH helps to solve this problem of perception, as occupants can better feel that the heating is on and operating.
Additionally, whilst the use of radiators can lead to cold spots developing in rooms – which often leads to the heating being turned up to compensate – UFH offers a more evenly spaced heat distribution throughout the room. This also reduces the chance of overheating.
For these reasons, UFH often delivers energy savings over equivalent large radiator systems. But, it is crucial that UFH – as with heat pumps – are correctly designed, specified and installed for rooms and properties. Standards (such as MCS) are needed to safeguard consumers and ensure that low temperature heating systems always deliver the emission and energy bill savings that they’re capable of. In addition, accessible and cost-effective upskilling needs to be made available to prospective installers so that a skilled workforce can develop to deliver
on the technology transition.
Policy ask #2
To unlock the benefits of low-temperature heating, ensure that good-quality heat pump and UFH installations are delivered:
Maintain standards such as MCS to ensure that any heat pump and/or UFH system that is installed (and potentially supported by policy) is correctly designed, specified and installed to deliver low emission and low cost heat for consumers.
Improve access to cost-effective upskilling for installers.
(b) Safety and space saving
The shift to low temperature heating means a shift to larger heat emitters. Large radiators extrude into rooms and take up valuable space in the home. UFH is by comparison integrated within the building construction, saving space and removing a potential hazard. Over 2.7 million people a year visit their local accident and emergency departments in the UK as a result of home accidents7.
The very young and elderly are especially at risk from falling into radiators or scolding themselves on a hot surface. These objects are typically made with steel and have sharp edges which are potentially hazardous.
The necessary move to low temperature heating means a move to larger heat emitters. Simply put, increasing the size of radiators in homes increases the risk of injury. A move to UFH instead of large radiators mitigates against this risk.
UFH also frees up valuable floor space. The Heat Emitter Guide8 includes an example sizing for a radiator to operate with a heat pump at 45°C flow temperature. The radiator is oversized by a factor of 3.1 (against the rooms required heat loss), and is over 1.6 metre in length.
Accounting for a reasonable assumption on the depth of the radiator from the wall, and assuming that a new-build semi-detached would require roughly 10 radiators, we estimate that such large radiators would occupy nearly 2.5 metres2 of floor space throughout the building. As it is built into the building fabric, UFH is a better solution, and frees up this valuable floor space.
Considering that in 2016, the average price commanded by houses (flats excluded) sold in England and Wales was £4,045/m2 (ONS9), then the value of freeing close to 2.5 m2 per
semi-detached home operating a heat pump through pairing with underfloor heating is clear.
Figure 7 compares our estimated costs and savings of a UFH system over large radiators in a new-build semi detached home. Whilst UFH is more expensive to install upfront (£369 more), our analysis suggests that efficiency benefits can be achieved which almost cancel out the upfront cost penalty over the assumed lifetime of the UFH/radiators10. The space savings when monetised are stark and considerable. If the average house price is taken from England and Wales, close to 2.5m2 of floor space is valued at roughly £10,000. This is a proxy and guide to the value of area that can be freed up by installing UFH into the building fabric, rather than specifying having large, heat-pump ready radiators in a new-build semi-detached home.
Figure 7 – comparison of the relative cost of UFH against large, heat-pump ready radiators in a semi-detached new build home
(c) Air quality
British people are thought to spend 90% of their time indoors. Indoor air quality is therefore an important issue. Allergens from mould and dust mites develop in humid and damp environments and can exacerbate respiratory illnesses such as asthma. With 5.4 million people in the UK currently receiving treatment for asthma, this is clearly an issue of importance.
UFH guards against the development of dust mites in carpets, rugs and other materials – as the systems keeps the flooring warm and lowers humidity. Additionally, and as described, the even distribution of heat produced by UFH prevents the development of cold spots.
Whilst radiators are more likely to circulate stuffy air around the room in an uneven pattern, the even distribution of radiant heat produced by UFH guards against the development of pockets of mould and dust mites.
(d) Lifetime of the system: infrastructure investment
Finally, UFH has a long lifetime and typically outlasts traditional radiator systems. Installing UFH is part of the investment in the building infrastructure, and will deliver dependable, evenly-spaced heat throughout a property over the long-term. This sort of long-term investment is needed if the UK is to cost-effectively meet its net zero emission targets by 2050, and in the case of UFH, can be achieved at a modest incremental upfront cost.
Summary: barriers to UFH deployment
One of the principal barriers to greater UFH deployment is the current setup of SAP, the assumptions and model that has a huge influence on the types of heat emitters installed in new and retrofit properties. The software currently uses data that is more than 20 years old to model the operation of UFH. Whilst the slower response times of UFH could have been problematic in older properties that needed instantaneous high temperature heat, the move to energy efficient new-build properties that can maintain a more constant and even temperature in the winter, needs to be better reflected in the SAP model. New build homes are warmer, and heating is only needed to top-up room temperatures by a few degrees. UFH is an ideal solution for these new properties, but instead is penalised for its slower response time in the software.
Low-temperature, baseload heating is more suited to the energy efficient properties envisaged in the Future Homes Standard that use electric heat pumps. It is time that the UK Government promotes a similar shift in the software that underpins and guides crucial building specification decisions. SAP needs to evolve to reflect the value of and move to low-temperate heating. The data and assumptions used for UFH need to be updated, as heating requirements, the building fabric and introduction of advanced controls mean that UFH has a greater role to play. This needs to be better reflected in SAP and building regulations.
Policy ask #3
Ensure that the additional benefits of underfloor heating (UFH) over radiators are properly understood and valued by building regulations, by:
Amending SAP to better reflect the additional benefits of UFH over traditional radiators. Reflect the move to low temperature and more consistent heating patterns in SAP. This is an important step that needs to happen to remove the barriers to take up of UFH and low temperature heating systems.
Variable | Value | Unit | Source |
Electricity carbon factor | Projected each year considered | kgCO2e/kWh | BEIS (download) |
ASHP 55°C flow temperature space heating efficiency 2 | 2.4 | SPF | CCC (download) |
ASHP 45°C flow temperature space heating efficiency | 3.0 | SPF | CCC (download) |
Non-traded central carbon price | Projected each year considered | £/tCO2e | BEIS (download) |
Estimated underfloor heating cost new build semidetached home | 30 | £/m2 | Nu-Heat |
Additional cost of UFH over traditional small radiators in a semi-detached new build | 16 | £/m2 | Nu-Heat and CCC (download) |
Additional cost of UFH over traditional large radiators in a semi-detached new build | 4 | £/m2 | Nu-Heat and CCC (download) |
Electricity price | Projected each year considered | p/kWh | BEIS (download) |
Typical new build semi-detached heat demand | 38.64 | kWh/m2/year | CCC (download) |
Typical new build semi-detached total floor space | 84.4 | m2 | CCC (download) |
ASHP lifetime | 18 | years | CCC (download) |
Size of large radiator needed for a heat pump operating at a 45°C flow temperature | 1600mm length, 700mm height, 135mm depth. 20mm from wall. | mm | ICAX (download) |
Annex: data inputs for figures 3-7
Disclaimer
Ecuity Consulting have provided analytical/modelling support for this paper. Any policy positions taken in this report reflect the views of Nu-Heat.
1 BEIS (2019) Final UK greenhouse gas emissions national statistics: 1990-2017
2 UKERC (2017) Unlocking Britain’s First Fuel: The potential for energy savings in UK housing
3 Current annual new-build rates of approximately 20,000 homes in Scotland, 160,000 in England, 9,000 in Wales and 6,000 in Northern Ireland
4 Heat Pump Association (2019) Delivering Net Zero: A Roadmap for the Role of Heat Pumps
5 BEIS (2018) Heat decarbonisation: overview of current evidence base
6 Vivid Economics and Imperial College (2019) Accelerated electrification and the GB electricity system
7 ROSPA (2019)
8 Available online here
9 ONS (2017)
10 60 years is the assumed lifetime of UFH and radiators here – based on CCC